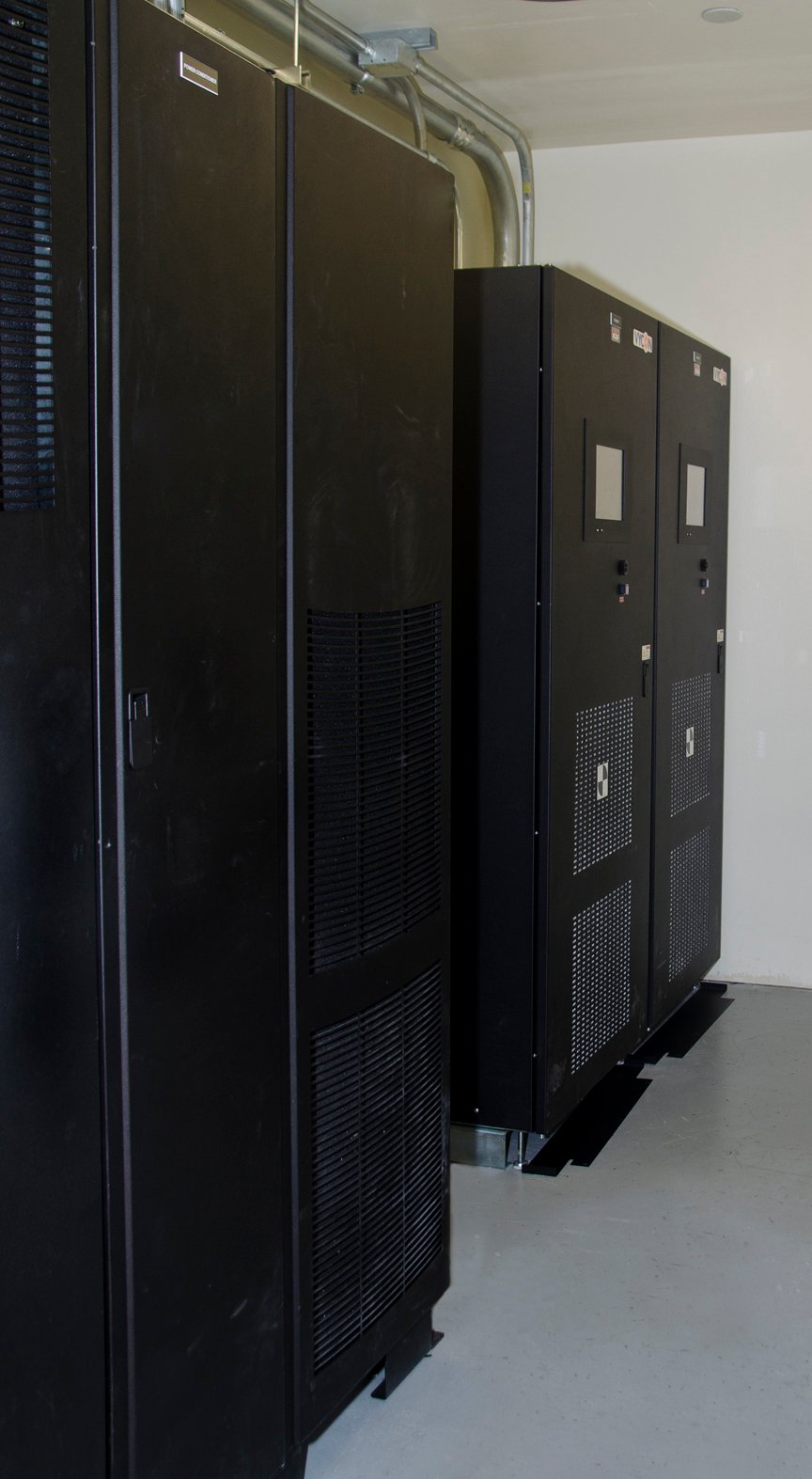
Over a 16-year period, air conditioning, high maintenance and frequent cell replacements of batteries can cost 3.5 times as much as a flywheel power system on a life cycle basis.
Whether it is a magnetic resonance imaging (MRI), computed tomography (CT) or other type of imaging system, reliable power protection is critical for the proper operation and uptime of imaging applications. But what happens if a healthcare facility suffers a power brownout, surge or outage? How do these events affect imaging equipment?
Without clean electrical power supplied to imaging equipment, costly problems can occur. In the case of MRI equipment, when there is a power interruption the MRI’s cryogen can begin to boil off. Depending on the design of the cryogen vent and the rate the cryogen is boiling off, the cryogenic gas discharge may freeze any accumulated water in the cryogen vent, blocking the pipe and increasing the odds for a cryogen vent breach in the event of a quench. Quenching refers to the events that occur when the liquid cryogens that cool the magnet coils boil off rapidly, which results in helium escaping very rapidly from the cryogen bath. Because a quench results in rapid loss of cryogens from the magnet, recommissioning the magnet is expensive and time consuming. If power is not restored to the vacuum pump, at some point the magnet will quench, discharging most of its remaining cryogenic gases.
Reliable Power Protection
As mentioned, when a power event occurs, the magnetic resonance required for imaging equipment can be compromised, causing serious damage. Accuracy can also be affected, resulting in frustrated patients who have to reschedule their appointments resulting in a potential decrease in referrals. To mitigate the effects of power interruptions, healthcare facilities have traditionally relied on the lead-acid batteries of uninterruptible power supplies (UPSs) to provide backup power. However, batteries are notorious for their reliability issues, large footprint and frequent maintenance and replacement.
More and more, facility managers are looking to not only increase power protection reliability, but also incorporate green technology to safeguard mission-critical applications. At the forefront of these types of technologies is the flywheel energy storage system. A flywheel is an environmentally friendly option for power protection, unlike traditional batteries that contain toxic lead- acid and require installation of safety spill containment.
Flywheel Energy Storage
A flywheel energy storage system is a mechanical battery that stores energy kinetically in the form of a rotating mass, replacing traditional backup batteries and performing in applications where batteries and other storage devices fall short. When needed during a utility outage, the energy stored by the rotating mass is converted to electrical energy through the flywheel’s integrated electric generator. The system then provides the direct current (DC) energy to the UPS until a stand-by diesel generator can be started. Once either the power from the utility is restored or the facility’s generator provides power to the input of the UPS, the flywheel system will recharge by taking some current from the DC bus of the UPS until it is restored to full charge speed.
How Flywheels Work
If there is a power outage or if the power coming in from the utility is “dirty,” the UPS can generate smooth, high-quality power from the flywheels. Many UPS systems depend on valve-regulated lead-acid (VRLA) batteries as their energy storage solution. However, lead-acid batteries degrade every time they are cycled (used), and one bad cell in the battery string can take out the others, rendering the battery bank useless. Due to their chemical nature, batteries generate heat and heat reduces battery life. Batteries can also release explosive gases that must be ventilated away. In addition, hazmat permitting, acid-leak containment, floor-loading issues, slow recharge times, lead disposal compliance and transport are important issues that have to be considered.
During a power event, flywheels can supply backup power seamlessly and instantaneously, providing instant power to the connected load exactly as it would do with a battery string. According to the Electric Power Research Institute (EPRI), 80 percent of all utility power anomalies/disturbances last less than two seconds, and 98 percent last less than 10 seconds. Additionally, the NFPA 99 regulation for healthcare facilities regarding emergency power systems stipulates that stand-by generators must be able to assume the power load within 10 seconds in the event of an outage.
Advantages of Flywheels
When compared to the traditional batteries in UPS systems, flywheels provide a number of advantages. One of the most important is dependability, providing up to 20 times higher reliability than lead-acid batteries. Predictable availability is a key component of this reliability – facility managers are continuously kept aware of the flywheel’s availability and status through built in monitoring and reporting, unlike a battery system which requires an add-on monitoring system. Even then, the state of availability is only really known once the battery is called upon to be used.
Another advantage of flywheels is the significant footprint savings. Flywheels can free up 50 to 75 percent of space that would otherwise be taken up by an equivalent power rated battery bank, thus lowering construction costs and allowing freed space to be used more productively.
Reduced cooling needs are another benefit of flywheel energy storage systems. Batteries require a firmly regulated environment for optimum performance and life. Flywheels on the other hand, do not require cooling, so not only do they take up less floor space, hospitals and imaging labs have much more flexibility on where to place the system. Flywheel energy storage systems also provide cost savings to users by offering a longer life span.
For example, Vycon’s VDC-XE flywheel energy storage systems have an expected 20-year life and a run time performance that never degrades within that time period. Flywheels can perform thousands of discharges and still the run time on the last discharge will be the same as the run time on the first. Batteries, on the other hand, typically require replacement every four years and run time performance degrades with age and usage. A longer life span results in a lower life cycle cost. Return on investment is typically within three to four years, and over a 15 to 20 year operation, flywheel total lifecycle cost is a fraction in comparison to batteries.
Finally, flywheel energy storage systems require minimal maintenance, relieving many headaches for facility managers. Because the flywheel utilizes a full levitation system with no mechanical bearings, there is very little in the flywheel module that needs to be maintained. Batteries, on the other hand, must be checked on a quarterly basis for leakage, cracks, capacity and corrosion.
Editor’s note: Frank DeLattre is president of Vycon Inc. The Vycon VDC-XE power backup system uses a flywheel hub that is formed from aerospace-grade steel, a high speed permanent magnet motor/generator, contact-free magnetic bearings that levitate and sustain the rotor during operation and a touch-screen control system that provides information on system performance. For more information visit www.vyconenergy.com.